The automotive landscape of the ’70s and ’80s was wild territory, friends – a time when gas crises, changing consumer tastes, and foreign competition forced American automakers to gamble everything on revolutionary new models. Remember those showroom floors with their plush carpeting and the smell of fresh vinyl as salesmen in wide lapels promised the future had arrived? For every Mustang or Corvette success story, there were spectacular failures that sent executives reaching for the antacids while accountants frantically revised quarterly projections downward.
1. The 1971 Chevrolet Vega

General Motors poured an astounding $200 million (nearly $1.3 billion in today’s dollars) into developing the Vega, constructing a dedicated factory in Lordstown, Ohio specifically for its production. The Vega represented GM’s first serious compact car effort to combat the growing Japanese imports, with chairman James Roche personally championing the project as the company’s salvation against the foreign invasion. Unfortunately, the engineering team rushed development, resulting in an aluminum engine block that warped, exterior panels that rusted within months, and quality control issues that would haunt GM’s reputation for decades. Indeed, Hagerty argues that this car could have been great, if only it hadn’t been rushed.
The fallout was catastrophic as warranty claims flooded dealers while resale values plummeted faster than a piano off a cliff. By 1977, finding a running Vega became something of a automotive unicorn hunt, with most examples having been junked due to terminal engine problems or rust that seemed to progress in real time before owners’ disbelieving eyes. The Vega debacle forced GM to completely rethink its approach to small cars, though the company would repeat many of the same mistakes with the Citation a few years later—proving that automotive amnesia was a genuine corporate condition.
2. The 1975 AMC Pacer
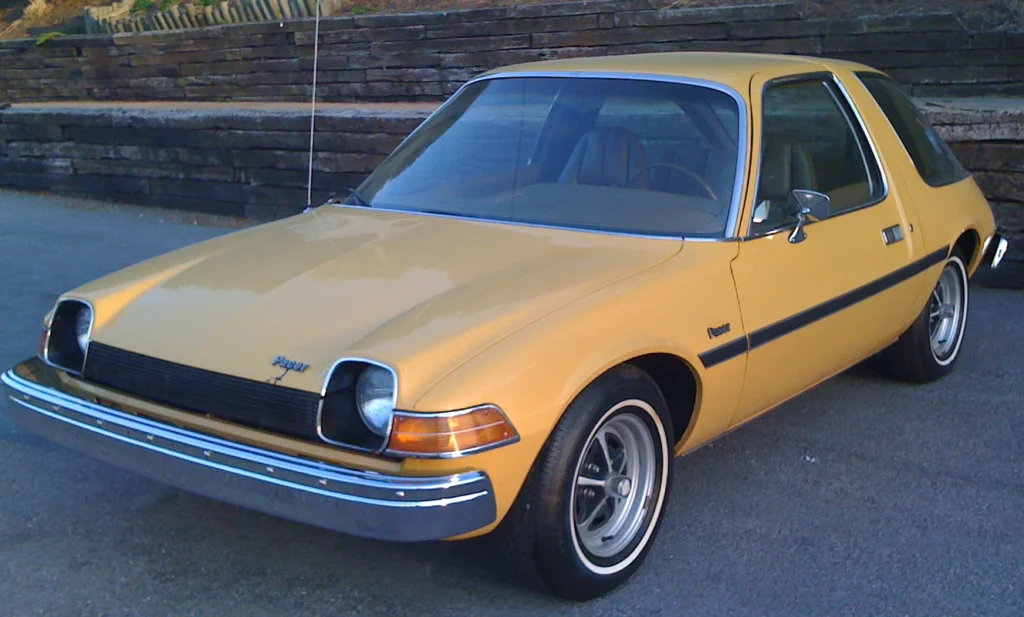
American Motors Corporation, always the underdog of Detroit’s automakers, invested nearly 40% of its development budget on the “first wide small car” that CEO Roy Chapin Jr. declared would revolutionize American automobiles. The fishbowl-like Pacer featured asymmetrical doors, massive glass areas, and a width approaching full-sized cars while maintaining compact length—design elements that AMC’s marketing department touted as “futuristic” but consumers ultimately found peculiar. The car was meant to use a lightweight Wankel rotary engine from GM, but when that deal fell through late in development, AMC was forced to shoehorn their existing heavy straight-six engine under the hood, destroying fuel economy and handling. History Channel recounts the exact moment the very last AMC Pacer drove down the assembly line.
Sales started strong with curiosity seekers but plummeted as practical realities set in—like greenhouse-effect heat from all that glass and gas mileage that would make an oil sheikh blush. The Pacer sucked desperately needed resources from the struggling company at precisely the wrong time, contributing to AMC’s financial troubles that ultimately led to its takeover by Renault and later Chrysler. In retrospect, the Pacer represented the last gasp of truly independent AMC engineering—a bold swing for the fences that unfortunately connected with nothing but air.
3. The 1981-1983 DeLorean DMC-12
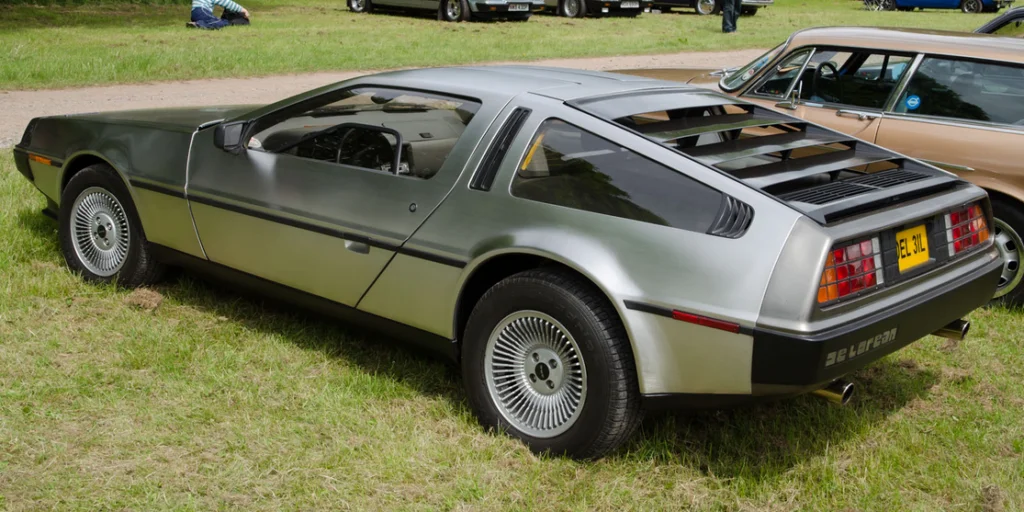
Former GM executive John DeLorean secured millions in British government funding to build his gull-winged stainless steel dream car in troubled Northern Ireland, gambling his reputation and fortune on bringing his vision to reality. The DMC-12 featured innovative design elements including unpainted stainless steel body panels, gull-wing doors, and a rear-mounted PRV (Peugeot-Renault-Volvo) engine—all adding up to a car that promised to revolutionize the sports car market. However, production problems plagued the vehicle from the start, with early models suffering from quality issues, underwhelming performance from the 130-horsepower engine, and an astronomical price tag of $25,000 (equivalent to around $80,000 today). Time Magazine characterizes the history of this car as short, yet every moment filled with chaos.
The company produced just over 8,500 cars before production halted abruptly in late 1982 following John DeLorean’s arrest on drug trafficking charges (he was later acquitted). The economic recession of the early 1980s delivered the final blow to a company already struggling with cost overruns and production difficulties that had ballooned the car’s development costs to astronomical levels. Though the DMC-12 found immortality as a time machine in “Back to the Future,” the original company burned through approximately $175 million in investments and loans before its spectacular collapse—proving that sometimes even the most dazzling automotive visions can’t overcome the harsh realities of business fundamentals.
4. The 1971-1977 Ford Pinto
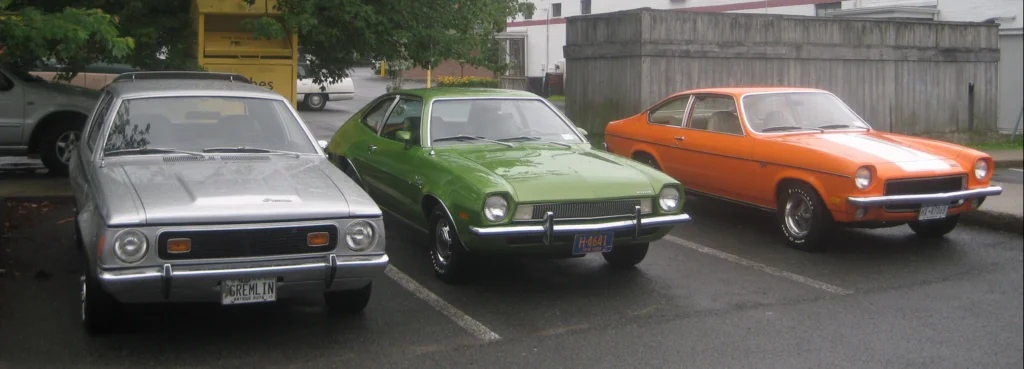
Ford rushed the Pinto from concept to production in just 25 months—half the normal development time—to compete with imports like the Volkswagen Beetle and Toyota Corolla that were eating into American sales. Lee Iacocca, Ford’s president at the time, insisted on the “2,000/2,000 rule”—the car had to weigh under 2,000 pounds and cost under $2,000, constraints that would later prove disastrous when safety concerns were sacrificed for speed and cost. Internal documents later revealed that Ford engineers discovered the fuel tank vulnerability during pre-production testing, but management made the infamous cost-benefit analysis determining that paying out settlements for burn injuries and deaths would be cheaper than the $11-per-car fix.
The Pinto’s reputation was forever tarnished after Mother Jones magazine published an exposé in 1977 detailing Ford’s knowledge of the fuel tank defect and the subsequent fiery crashes. While the Pinto sold well initially with over 3 million units moved, the recalls and lawsuits cost Ford dearly—not just financially, but in terms of consumer trust that took decades to rebuild. The Pinto case became a textbook example of corporate ethics failure taught in business schools nationwide, showing how one model could not only fail commercially but become a liability that haunted a company’s reputation long after production ended.
5. The 1975-1980 Triumph TR7
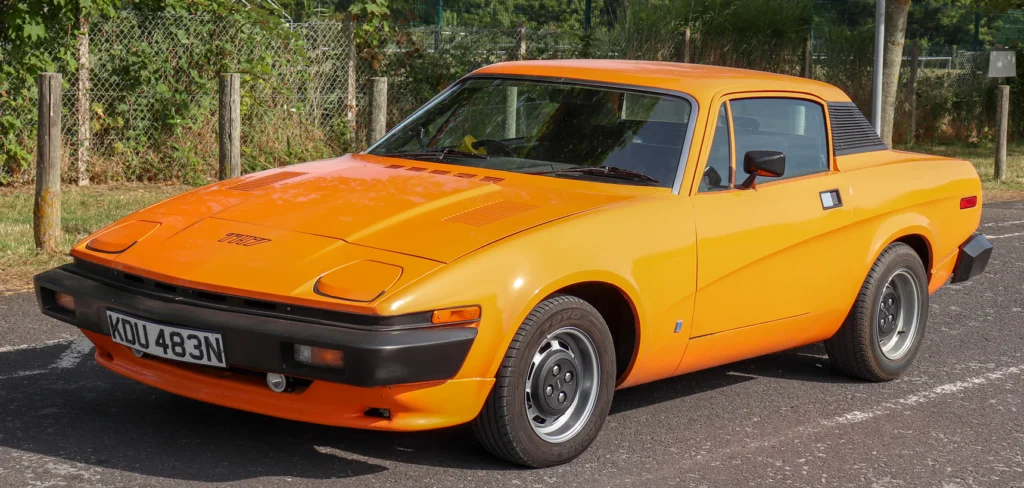
British Leyland, already struggling financially, invested heavily in the TR7 as their “future-proof” sports car that would revitalize the company’s image and capture the lucrative American market. The wedge-shaped design represented a radical departure from Triumph’s traditional styling, with pop-up headlights and a fixed roof that horrified traditionalists but was intended to meet anticipated U.S. rollover safety regulations that never actually materialized. Production problems began immediately at the strike-prone Speke factory in Liverpool, with early cars developing rattles, leaks, electrical failures, and engine problems that quickly earned the model the unfortunate nickname “The Shape of Things to Break.”
The TR7 suffered from having four different production locations during its troubled lifespan as British Leyland desperately shuffled manufacturing from one problem-plagued factory to another. Though nearly 115,000 units were eventually produced, the model never recouped its development costs, and the planned family of vehicles based on its platform was largely abandoned as British Leyland circled the drain financially. The TR7 represented the last gasp of the independent British sports car industry—a desperate swing that missed so badly it contributed to the collapse of the entire British Leyland conglomerate and the end of several historic marques.
6. The 1974-1978 Chrysler Cordoba
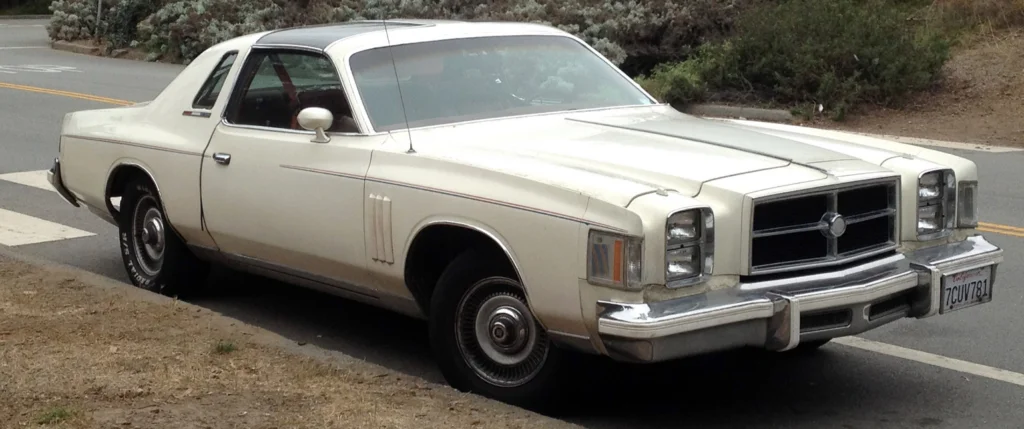
Chrysler bet heavily on the personal luxury coupe market with the Cordoba, investing nearly 60% of their limited development resources into a model that chairman Lynn Townsend insisted would save the struggling company. The Cordoba became famous for Ricardo Montalban’s silky television delivery about its “rich Corinthian leather”—an entirely fictional marketing term that nonetheless became part of the cultural lexicon. Though initially successful with over 150,000 units sold in its first year, the Cordoba represented a catastrophic strategic error for a company desperately needing economical small cars as the second oil crisis loomed.
The model’s timing couldn’t have been worse as fuel prices skyrocketed just as Chrysler had committed to the gas-guzzling luxury segment. By 1979, Chrysler was forced to request a controversial government loan guarantee to avoid bankruptcy, with the Cordoba’s resource drain frequently cited in congressional hearings as evidence of the company’s strategic mismanagement. The Cordoba came to symbolize Detroit’s tone-deaf response to changing market conditions—a beautiful but thirsty dinosaur that accelerated Chrysler’s financial collapse and necessitated Lee Iacocca’s dramatic company reinvention around the K-car platform that finally delivered the efficient front-wheel-drive vehicles Americans actually wanted.
7. The 1976-1987 Maserati Biturbo
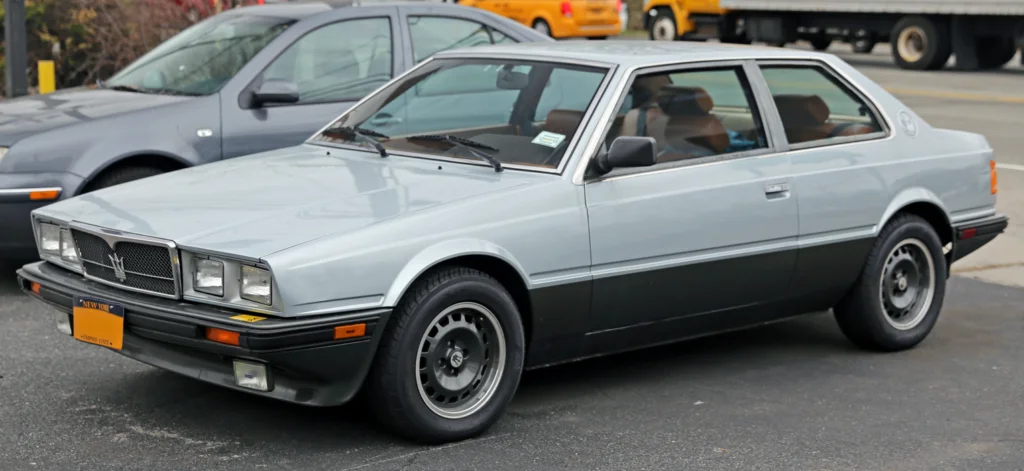
Alejandro de Tomaso bet Maserati’s future on the Biturbo—intended as a “mass-market” luxury sports car that would transform the struggling exotic brand into a volume manufacturer. The Biturbo represented the first twin-turbocharged production car, packing impressive technology and performance specs into a relatively affordable package that promised to bring Italian exotic flair to upper-middle-class garages across the world. Unfortunately, combining complex twin-turbo technology with Maserati’s already questionable reliability and adding cost-cutting measures created a maintenance nightmare that could reduce grown men to tears.
Electrical gremlins, vapor lock, cooling system failures, and turbocharger issues turned many owners’ dreams into expensive nightmares within months of purchase. The Biturbo actually sold relatively well initially with around 40,000 units produced across all variants, but catastrophic depreciation and word-of-mouth warnings eventually caught up with the model. The Biturbo experiment nearly killed Maserati completely before Ferrari took control of the company in 1997 and began the long process of rebuilding the brand’s shattered reputation—proving that sometimes even the most prestigious badges can’t overcome the reality of poor execution.
8. The 1974-1978 Ford Mustang II
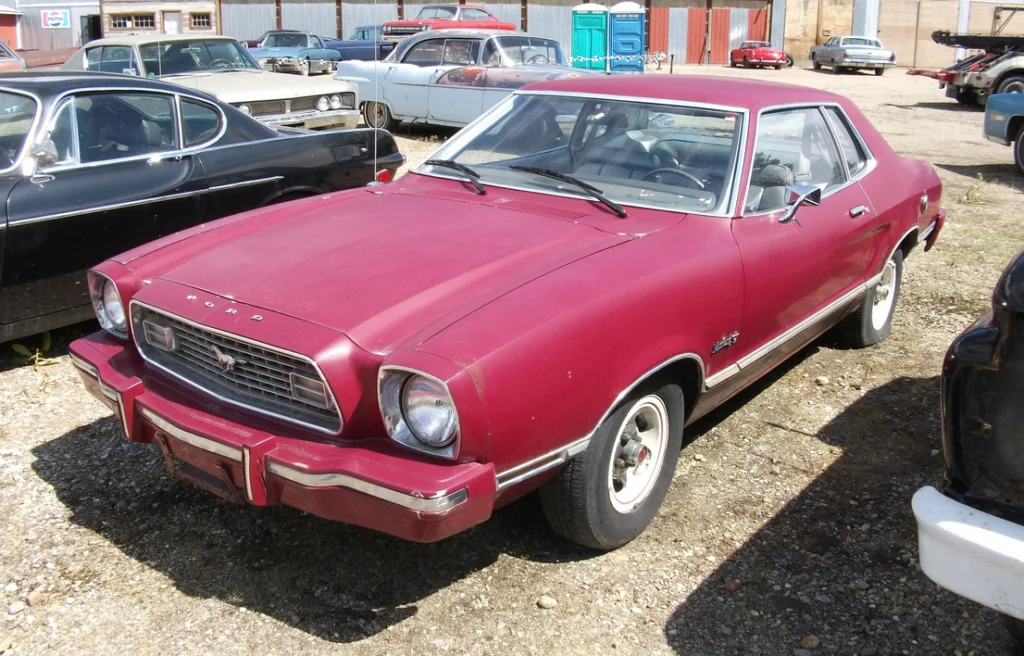
Ford, panicking over skyrocketing gas prices and declining muscle car sales, made the controversial decision to reinvent their pony car icon as a Pinto-based compact—a move that president Lee Iacocca insisted would save the nameplate from extinction. The Mustang II was significantly smaller than its predecessor, offered with a four-cylinder engine for the first time, and removed virtually all performance options in favor of luxury appointments like vinyl roofs, opera windows, and plusher interiors. While Ford’s marketing trumpeted the new direction as “right for the times,” Mustang enthusiasts were horrified to find their beloved performance icon transformed into what many derisively called “a secretary’s car.”
The decision split the automotive world, with traditional Mustang fans abandoning the nameplate while a new demographic embraced the smaller, more efficient package. Though the Mustang II actually sold well with over 1.1 million units moved during its five-year run, the model nearly destroyed the performance credibility that had defined the nameplate since 1964. The damage to the Mustang’s performance image took Ford nearly a decade to repair, requiring the introduction of the Fox-body platform and the gradual return of V8 power to restore enthusiast faith in the brand—making the Mustang II a commercial success but a strategic blunder that’s still debated in automotive circles today.
9. The 1974-1975 Bricklin SV-1
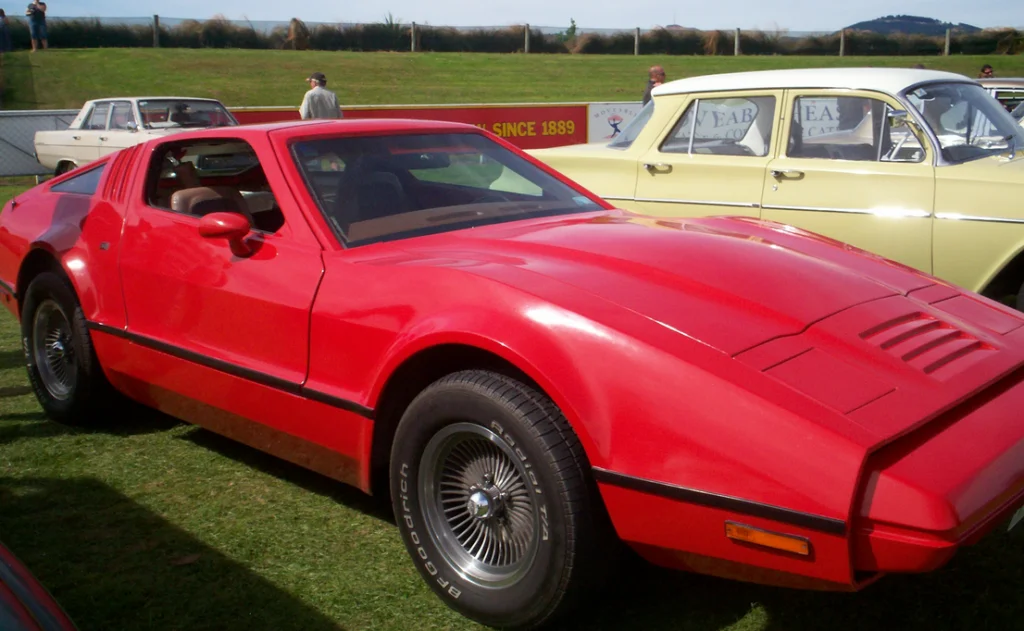
Malcolm Bricklin, fresh off introducing Subaru to America, convinced the Canadian government to invest millions in his vision for a safety-focused sports car to be built in the economically disadvantaged province of New Brunswick. The SV-1 (Safety Vehicle One) featured an integrated roll cage, energy-absorbing bumpers, and gull-wing doors—all wrapped in a sleek fiberglass body that couldn’t be ordered in red because Bricklin thought the color encouraged speeding. Production problems plagued the venture from the start: the electro-hydraulic door system frequently trapped occupants inside when batteries died, the acrylic body panels warped in heat, and the fit and finish would have embarrassed manufacturers of children’s toys.
With each car reportedly costing $16,000 to build but selling for only $9,780, the company hemorrhaged cash at a spectacular rate. After producing just 2,854 cars and burning through approximately $23 million in Canadian government funds, Bricklin Vehicle Corporation went spectacularly bankrupt in 1975. The Bricklin saga demonstrated how even the most charismatic entrepreneurs could fall victim to the harsh realities of automotive manufacturing costs, leaving New Brunswick taxpayers holding the bag while Malcolm Bricklin moved on to his next venture—importing Yugos to America, which would become another legendary automotive misadventure.
10. The 1980-1988 Rover SD1
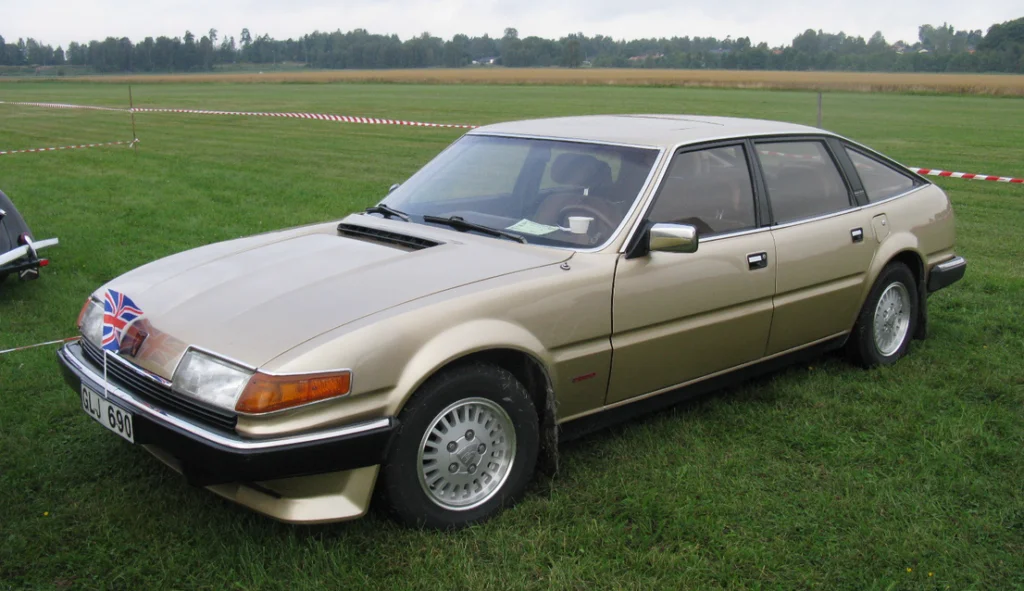
British Leyland invested £95 million (an enormous sum for the struggling company) in the sleek, Ferrari Daytona-inspired SD1 as their flagship model intended to compete with BMW, Mercedes, and Jaguar in the executive car market. The SD1 won European Car of the Year honors and received praise for its innovative hatchback design, V8 performance, and interior space—looking for all the world like British Leyland’s long-awaited comeback vehicle. However, catastrophic quality problems quickly emerged: cars leaked in rain, electrical systems failed randomly, paint literally fell off panels, and engines developed alarming tendencies to separate from their mounts.
The problems stemmed from British Leyland’s disastrous decision to build the car in a brand-new, automated factory at Solihull where untrained workers struggled with unfamiliar equipment. By the time British Leyland improved quality in later production years, the damage was done—European executives wouldn’t touch the car, and exports to the crucial American market were abandoned after just a few thousand units. The SD1 debacle accelerated British Leyland’s downward spiral, with the British government eventually forced to nationalize the company completely—turning what should have been the company’s savior into yet another nail in its corporate coffin.
11. The 1986-1992 Cadillac Allante
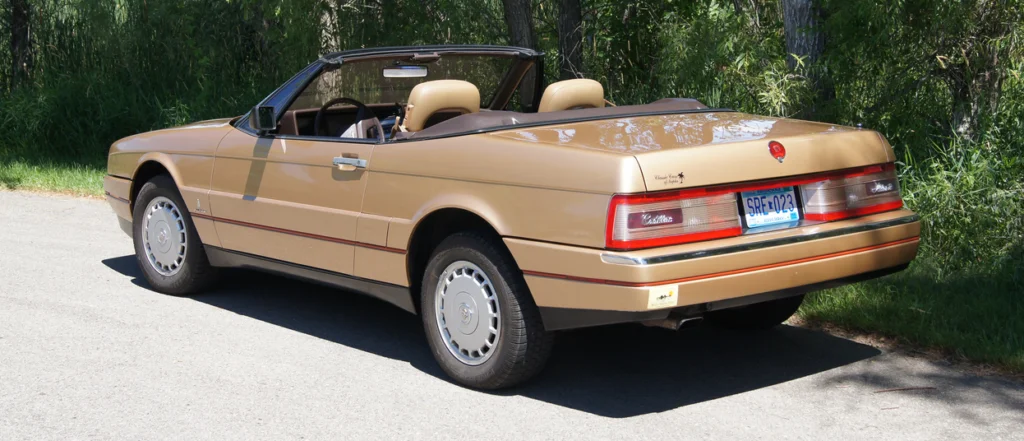
General Motors, determined to create a Mercedes SL competitor regardless of cost, arranged for Pininfarina in Italy to design and build the Allante bodies, which were then flown 4,600 miles by specially modified 747s (dubbed the “Air Bridge”) to Detroit for final assembly. Each transatlantic body shipment cost GM approximately $8,000 per car—before a single mechanical component was installed—helping push the development cost to over $500 million (more than $1 billion in today’s dollars). The logistics nightmare was compounded by quality problems caused by bodies built to Italian specifications not properly matching American-made components, creating assembly headaches that plagued the model throughout its production.
Despite its astronomical price tag of nearly $60,000 (equivalent to about $150,000 today), the Allante initially came with an underwhelming V8 engine and front-wheel drive—specifications that luxury sports car buyers found thoroughly unimpressive. Sales never approached GM’s targets, with only 21,430 units sold over six years against a projection of 6,000 units annually, making each sale a financial loss for the company. By the time Cadillac finally gave the Allante a proper engine with the 1993 Northstar V8, GM had already decided to pull the plug—ending production just as the car was finally becoming competitive and cementing the model’s reputation as a textbook example of corporate hubris.
12. The 1982-1988 Pontiac Fiero
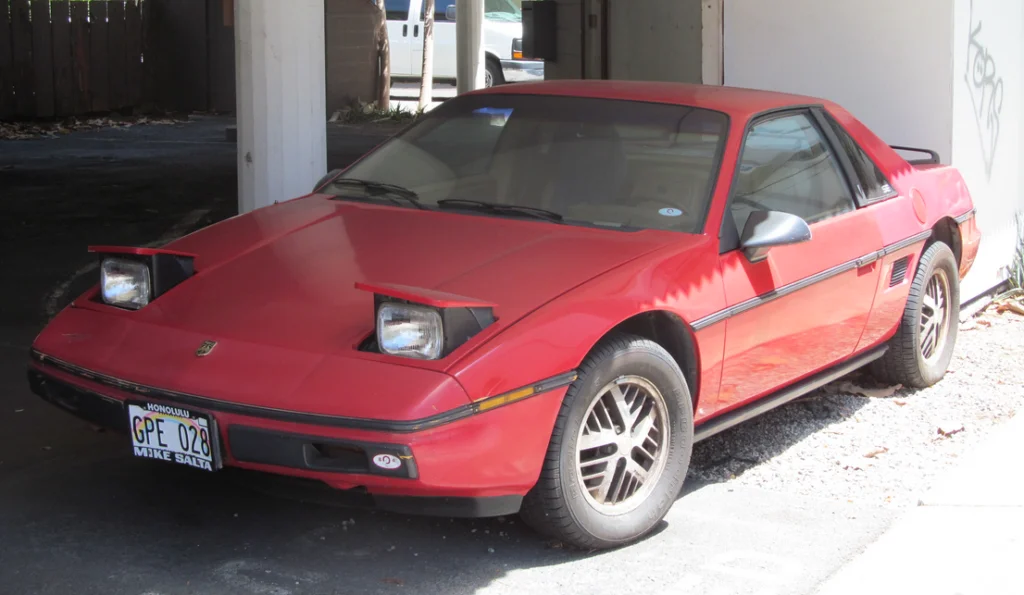
General Motors approved the Fiero project by misleading its own board, presenting the mid-engine sports car as a fuel-efficient commuter vehicle rather than the Corvette competitor engineers secretly intended to build. The deception forced designers to use existing mechanical components from GM’s parts bin, resulting in mundane Chevette front suspension and clunky X-car derived steering that compromised the handling of what was marketed as a sports car. After slashing the original $400 million development budget, Pontiac cobbled together the Fiero using so many existing parts that engineers nicknamed it “the corporate parts bin special,” resulting in a car that looked exotic but performed like an economy car wearing a costume.
The model initially sold well but quickly developed a reputation for catastrophic engine fires, leading to recalls and a permanently tarnished image. By the time Pontiac finally engineered a proper suspension and more powerful engine for the 1988 model year, GM management had already decided to terminate the program. The crushing irony of the Fiero saga was that just as the car finally became the sporting machine it was always meant to be, GM pulled the plug—killing the model after investing $300 million in improvements and manufacturing facilities, only to abandon the project just as it was becoming competitive.
Looking back on these automotive gambles from our comfortable perch in 2025, it’s easy to chuckle at the missteps, but each represents dreams, careers, and billions in investments that went spectacularly sideways. These weren’t just corporate failures—they were part of our collective automotive experience, as familiar to us as shag carpeting and wood-paneled station wagons. While the companies have largely recovered (those that survived, anyway), these cautionary tales remind us that even the mightiest automakers aren’t immune to spectacular miscalculations—something worth remembering next time a manufacturer promises they’ve reinvented the wheel.